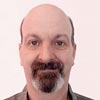
January 31, 2017
When companies are implementing a Quality Management System (QMS) using the requirements of ISO 9001:2015, there is often confusion when it comes to the topic of validation. People can get confused when talking about the difference between design verification and design validation, or discussing what is considered design validation as opposed to process validation. Understanding validation can be complicated.
So, what is process validation and how does it work? When used properly, validation can help you to ensure that your processes are actually doing what you intend them to do, even when you can’t check the product or service coming out of the process during real product or service realization.
For a better understanding of the differences between processes and procedures, see this article on ISO 9001:2015 process vs. procedure – Some practical examples.
Process validation, quite simply put, is the act of controlling a process and actually performing the necessary tests to ensure that the process can, in fact, perform according to the requirements it is designed to meet. In the ISO 9001:2015 standard Clause 8.5.1 on control of production and service provision, there is a requirement for you to have controlled conditions for “the validation, and periodic revalidation, of the ability to achieve planned results of the processes for production and service provision, where the resulting output cannot be verified by subsequent monitoring or measurement.”
This means that a process needs to be validated if you will not be able to check if the product or service is compliant with input requirements. An example might be a soldering process or welding process where you cannot check the strength of every weld during your regular production without damaging or destroying the parts.
As you can see, not every process is required to undergo a validation as per ISO 9001:2015, so if you have a process where validation is not required per ISO 9001, you can still choose to validate the process. For instance, you may want to validate a process in order to reduce a complex or costly inspection of the product or service after the process, even if you could check that the outputs meet the input requirements. Which processes you validate is determined by you and your needs.
The only way to really validate a process is to perform it, check that the process parameters can be met during the trial use through measurements, and then perform a full check on the products or services that come out of the process to ensure that they meet the requirements. If there is no other way to verify, you may need to actually destroy parts in order to perform the inspection for the process validation, such as cutting apart a weld to ensure it is done correctly – something you could not do on every part that came out of the process. While ISO 9001 does not specify which records need to be kept, you will need to keep whatever records you find necessary to show that the process was validated and that it worked.
It is important to remember that process validation needs to represent how the process will actually occur. If you try to validate in a manner that does not represent how the actual process will run, then you could run one order through a process and find that it works well, and then when you use the process at a daily production rate of 100, you may find that the process is not actually capable of performing to meet the requirements that are set out for it.
The easiest way to validate a process is to set the process up in the manner it will be used, and perform an expected production run of the process: regular operators, tooling, equipment, environment, facility, gauges, rate, etc. Once you have proven that the process can run correctly without special attention above and beyond what you would normally put in place, then you can determine that the process will do what you need it to do when you start to use it.
This will also allow you to determine if there are special skills needed to perform the process, such as training for solder operators or welders, and this can become part of your process definition. When you have successfully completed your process validation, you will know what process parameters need to be in place, including what operator training and certifications need to be obtained, in order for your process to run successfully.
Validation can be complex, but when used properly, it can save you time and money in the long run by making your processes more reliable, and less reliant on inspection and post-process verification of products and services to ensure acceptable product and service creation. Knowing your process will successfully perform the function it is intended to do will help reduce your nonconforming products and make it easier to demonstrate in an audit that you have control of the processes for creating your products and services.
In addition, unless you know that a process is consistent, you cannot tell if an improvement was successful, so a validated process can be a good starting place for process improvements, leading to time and money savings for your company, and other benefits for your customers and employees. By making sure your processes are performing as designed, you can drive the improvements you want from your QMS implementation, and work towards continued success for your company.
For a better understanding of the ISO 9001:2015 requirements regarding process validation, check out this free online training: ISO 9001:2015 Foundations Course.