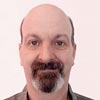
November 3, 2015
ISO 9001:2015 includes some changes in product realization, but what are some practical examples of how these requirements can be implemented? Section 8.5 of the new standard discusses the requirements for product and service provision, and it is here that we need to look for such examples of how we can meet these requirements.
For proper production and service provision you need to have controlled conditions, but these can vary depending on company need. What documented information is needed to define the characteristics of the product or service, as well as the activities to be done and the outcomes you expect? Do you need detailed drawings, extensive training, or even signage at the work stations? How will you monitor the activities to ensure the acceptance criteria are met, and how often? What competence and qualifications do your people need when creating your product or service? Most importantly, how will you identify product that can be released; do you need extensive testing and inspection, or can an operator decide that a product or service is acceptable to release for use?
Not every product or service requires identification and traceability, but if this is needed, how will you identify your outputs? Some companies label their parts with unique serial numbers that can be traced to all data related to that part, while others apply batch traceability where it is needed. I have even heard of a company where the employees actually identified on the assembled parts themselves who installed each part. You need to determine what needs to be done, and how you will do it to suit your needs. Note that this includes temporary identification to make sure that products do not become mixed up between processes in your organization.
Do you get materials, components, tools, or intellectual property from your customers that are needed to provide your products or services? If so, then you need to have methods in place to care for these items when they are under your control, and to make sure they are not incorrectly used. Do you need a formal procedure so that everyone follows the same rules with customer property? Do you need to label the customer property? Are there other things you could do to ensure that customer property is not damaged or misused?
For the process outputs, be they products or services, what do you need to do to make sure they maintain their conformity to requirements? Do you need to keep parts in bins to protect their integrity? Do you need a way to identify how complete a service is when it is handed off from one employee to another to make sure that everything gets done before the service is completed for the customer?
Do you have a need to provide service for your product or service post delivery? Some things that will affect this are the risks associated with the product or service, customer feedback, regulatory requirements, and the use and lifetime of the product or service. Do you need to follow up on a product or service after several months to ensure it is still functioning properly, or does this not matter? Do you need to do anything to ensure proper recycle or disposal of your product when it is at the end of its life, such as supplying disposal services? For instance, there are several examples around the world where drink bottles require a deposit and can be returned for cleaning and re-use rather than recycling and disposal.
Finally, if you need to change anything, especially unplanned changes, you need to make sure that the change is reviewed adequately to safeguard against problems in the conformity of your product or service due to the change. Do you need to do a risk assessment, or is the risk well known for the change you need to do? Is this change for all future products and services, or just this one delivery? You need to plan out the change before making it to prevent problems.
The main point of the ISO 9001 requirements for product and service provision is planning. If you want to ensure that problems are controlled, you need to understand what requirements are imposed on you from external parties or even internal needs. By properly planning your production and service processes, you will have fewer errors due to misunderstanding, and therefore fewer problems. Control of the creation of your product or service is the main reason you are implementing ISO 9001, so plan these processes out well.
If you are embarking on your transition to ISO 9001:2015 it would help to read this white paper on the Twelve-step transition process from ISO 9001 2008 to 2015 revision.